Passive Fire protection is a vital factor in reducing risk is to provide physical barriers to the spread offire within the building by dividing it into a series of compartments bounded by fire resisting walls and floors. This concept is fundamentally effective and generally reffered to as "compartmentation"', is fire-proofed to an optimum level to prevent the spread of fire, smoke and toxic gasses.
Fire Safety In The Building Industry
Like Buildings, fire control is a continually evolving science that general starts with the idea that a bucket of water or sand in the right hands at the right time and place can make the difference between a minor incident and a major disaster. Unfortunately, we live in a built environment that is considerably more complicated.
The risk of a fire defends on a building's use, location, size, occupants design and construction. In general, the larger the building, the greater the risk to life and property. The protection of the structral frame, the enclosure and protection of vertical and horizontal openings, effective fire-stopping at junctions, protection of service penetrations, use of low flame spread finishing materials and non-combustible materials are all important considerations.In addition, the fire performance of external walls and roofsand their proximity to other buildings are essential factors to consider in the prevention of spread of fire between buildings. All these measures are referred to as"proactive" fire protection for they are systems that do not require power or water to operate in the event of a fire. They protect on demand, as and when necessary.
What Is Proactive Fire Protection?
PROACTIVE FIRE PROTECTION products and systems are tested by indepently approved testing athorities under standard test conditions. The fire performance standard and terms most relevant to the materials and elements of construction described in this handbook are as follows.
Fire Testing Methods: Fire Curves
The fire performance of any system will vary epending on the heating conditions it is xpressed to. Different national and international fire curves have been developped to simulate fires carried out in fire test furnaces, by recognised national organisations.
These include:
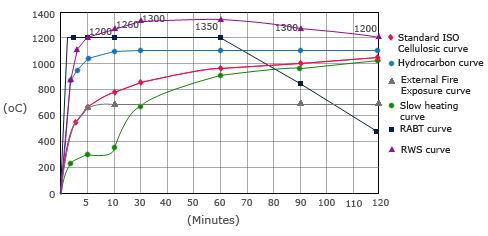
1. The Standard Cellulosic
Time- Temperature Curve
The fire performance of any system will vary depending on the heating conditions it is expressed to. Different national and international fire curves have been developped to simulate fires carried out in fire test furnaces, by recognised national organisations.
This include: This ISO-based curve is used in standards throughout the world, including BS476, AS1530, ASTM, and the new European Norm(EN). It is a model of a ventilation controlled natural fire, i.e., fire in a normal building. The temperatureincrease after30 minutes is 842oC.
2. The Hydrocarbon Curve
This curve is a simulation of a ventilated oil fire with a temperature increase to 1110oC after 30 minutes. The Hydrocarbon Curve is applicable where petroleum fires might occur in an open environment, i.e. petrol or oil tanks, certain chemical types etc. In fact, although the Hydrocarbon Curve is based on a standardised type fire, there are numerous types of fire associated with petrochemical fuels which have wide variations in the duration of the fire, ranging from seconds to days.
3. The RABT Curve
This curve was developed in Germany as a result of a series of test programmes (e.g. the Eureka project) into the effects of fire within enclosed spaces such as road and rail tunnels. In these situations, the inability of the heat to dissipate in to the atmosphere, and the flue like effect of the tunnel geometry feeding air to a fire (similar to a blacksmiths bellows) results in much faster fire growth and higher temperatures. In the RABT Curve, the temperature rise is very rapid, up to 1200oC within 5 minutes. The duration of the 1200oC exposure is for either 30 or 60 minutes, depending on type of tunnel (e.g. road or rail). The temperature then begins to drop as this curve has a defined "cooling of" period of 110 minutes.
4. The RWS Curve (Rijkswaterstatt)
This model of a petroleum- based blaze is a 300MV load fire occuring within an enclosed area such as a tunnel. Developed in the Netherlands specifically for use in tunnels, it is internationally accepted. For instance, the 2007 edition of NFPA 502 will require tunnel stuctures to be protected to the RWS level of exposure. The temperature increase after 30 minutes is 1300oC with a peak of 1350oC.
5. The External Fire Exposure Curve
This model is for fire exposure external to a building and open to the atmosphere, where there are additional possibilites for heat dissipation resulting in lower fire temperatures. There is a consequential lower level of heat exposure. Temperature increase is approximately 680oC after 20 minutes and remains constant throughout.
6. The Slow Heating Curve
This curve simulates a slow growing fire. It is basically a combination of two curves, one for the first 21 minutes reprsenting the smouldering effect of materials and one for subsequent periods representing the growth of the fire towards flashover.
7. Furnace Pressure
As wellas controlling the exposure temperature, the test standards require that the air pressure within the test furnace is maintained at a positive level in an attempt to create a worse case scenario and force hot gases and flame though the specimen under test. In addition, thermocouples are fixed to the unexposed face of the specimen to measure the performance of the system against the transfer of heat from the hot to the cold face of the specimen.